Concrete means spending. Polyethylene means investing.
Today, concrete manholes are much more widespread than polyethylene ones: a fact that can be explained by habit and the large number of concrete prefabricators present in the territory. In the most advanced and developing countries, however, where technical and economic factors are analyzed without prejudice, the most widespread are precisely polyethylene manholes. Thanks to the KMC manhole, there are no longer any reasons to discriminate against polyethylene manholes:
it is a product that exists and has been used successfully throughout the world for over 30 years. In the piping sector, for example, the trend is the opposite: the problems arising from concrete pipes are recognized by everyone. Few people know that both for concrete and for polyethylene, strict reference standards must be respected and even less known is the fact that in all European markets for CE-marked construction products, the declaration of conformity has been replaced by the declaration of performance. The manufacturer must not only have complied with the standards, but must also have carried out all the required tests before placing the product on the market. Furthermore, the checks must be repeated periodically.
The reference standard for concrete manholes is EN 1917 2004 “Manholes and inspection chambers in non-reinforced concrete, reinforced with steel fibres and with traditional reinforcements” together with the national standard UNI 11385. The reference standard for polyethylene manholes is EN 13598-2 2009 “Specifications for inspection manholes accessible to personnel and for inspection chambers, for underground installations in traffic areas and at depth”. Both standards specify the performance requirements and describe the test methods. The main characteristics resulting from the tests must be:
- Mechanical resistance
- Load capacity of any pre-assembled steps
- Water tightness
- Durability – operating conditions appropriate to the intended use
The manufacturer must prepare, store and deliver upon request all documents certifying the tests carried out.
Polyethylene
Concrete Manhole
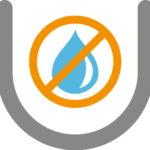
Perfect hydraulic resistance also at the presence of groundwater. The rubber seals and the structure ensure tightness up to 0.5 bar.
The KMC inspection chamber eliminates the parasite water in the duct and prevents the pollution of the water table.
HYDRAULIC RESISTANCE
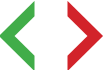
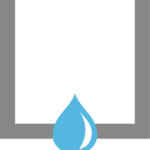
Several studies have shown that more than 50% of the concrete inspection chambers are not watertight immediately after they are installed.
The concrete inspection chamber does not ensure water tightness.
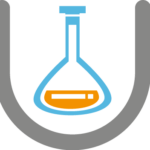
High chemical resistance, non-toxicity, low hygroscopic adsorption, low friction coefficient, good resistance to wear, wide range of temperatures of utilization.
The KMC inspection chamber is not aggressed by chemicals.
CHEMICAL RESISTANCE
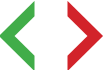
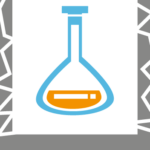
Both the strong and the weak acids are harmful to the cement paste. The hydrogen sulphide, which is present in all the common sewage systems, corrodes the inspection chamber. In these conditions, the concrete loses 5 to 10 mm of thickness per year.
The concrete inspection chamber starts corroding as soon as put into service.
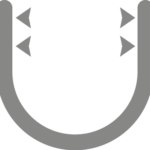
Very high static resistance thanks to the special patented network ribs.
The KMC inspection chamber will not break.
STATIC RESISTANCE
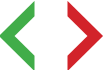

High static resistance due to the rigidity of the structure.
The concrete inspection chamber difficultly breaks.
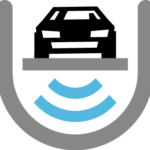
Very high dynamic resistance, thanks to the elastic features of polypropylene: all the vibrations caused by traffic and micro-settlements are adsorbed.
No cracks generate in the KMC inspection chamber.
DYNAMIC RESISTANCE
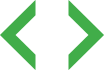
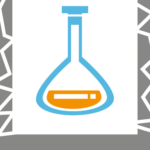
The high rigidity of the structure, which ensures its good static resistance, may generate cracks in the structures and – mainly – displacements of the junctions because of the continuous vibrations due to the traffic and to the micro-settlements.
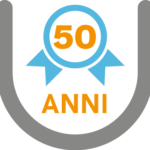
A 50-year performance simulation confirms the return time adopted for the design of the inspection chambers and of their components
In 50 years, the KMC inspection chamber shall still be in service and performing as the first day.
DURATION
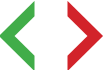
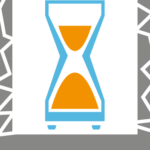
The continuous chemical attack of the agents contained in the sewage does not allow predicting the actual duration of the part.
The concrete inspection chamber difficultly lasts as much as the average life span specified for the sewage network.
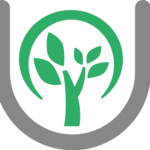
Significant studies have shown that – compared to the concrete inspection chamber – to produce a polyethylene inspection chamber – 75% less of CO2 s released into the environment. These data do not yet take into account the factors of transport, maintenance, efficiency, duration in time and recyclability at the end of its life span.
The KMC inspection chamber respects the environment.
ENVIROMENT
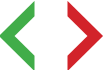
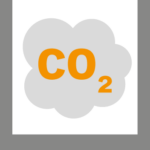
Important studies have shown that – compared to the polyethylene inspection chamber – to produce a concrete inspection chamber 400% more of C02 is released into the environment. These data do not yet take into account the factors of transport, maintenance, efficiency, duration in time and recyclability at the end of life span.
The concrete inspection chamber does not respect the environment.
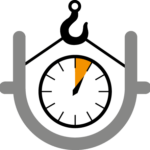
The handling and installation time is minimized. There is no need for any heavy means.
The KMC inspection chamber can be installed in 15 minutes.
FAST INSTALLATION
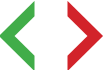
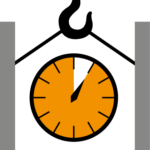
The handling and installation time is very high. Heavy, very costly means are required.
The concrete inspection chamber takes two hours to be installed and further sealing and finishing actions are required.
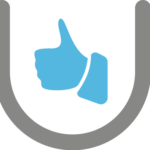
Anyone can install the KMC inspection chamber, by simply following the instructions, or even just intuitively, with no need for special equipment and with few people.
Anyone can install the KMC inspection chamber.
EASY TO INSTALL
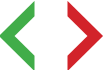
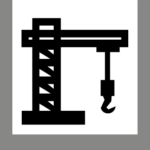
The installation of the concrete inspection chambers calls for specialized manpower and for the assistance of several operators.
The concrete inspection chamber calls for qualified personnel and a large amount of assistance.
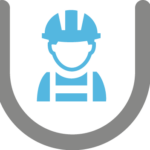
Significant reduction of the risk of site accidents thanks to the lightness of the part.
The KMC inspection chamber is the ideal partner for safety on site.
SAFETY ON SITE
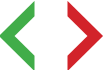

The risk for the operators is very high during both handling and installation.;
The concrete inspection chamber represents high risk for the site operators.
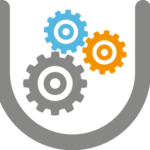
Fittings and height of the inspection chamber can be adapted on site with the support of simple tooling available in any warehouse.
The KMC inspection chamber is a champion of versatility.
ADAPTABILITY
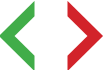
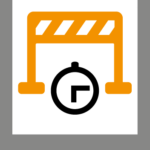
All the changes to be applied on the concrete inspection chambers call for many working hours and costly equipment.
The concrete inspection chamber is very complicated to be adapted.
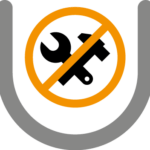
Significant reduction of the cleaning and restoration actions.
With the KMC inspection chamber, you tend to forget maintenance.
MANTENAINCE
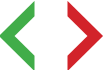
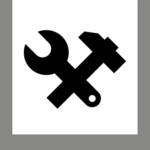
Corrosion, square edges that generate clogging, infiltrations and low roughness call for frequent costly actions of extraordinary maintenance.
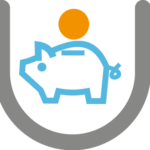
Impermeability, chemical resistance, static and dynamic resistance, longevity, easy handling, reduction of the risks on site, adaptability, reduced maintenance: all this factors contribute to the cost-effectiveness of the polyethylene inspection chamber.
The KMC inspection chamber is technically and economically advantageous and can be considered an investment.
SAVING
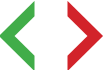
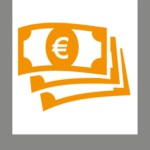
Infiltrations, low chemical resistance, vulnerability to vibrations, unpredictable life span, difficult handling and installation, the high risk on site, the difficult adaptability, the need of frequent maintenance are factors which affect the cost-effectiveness of the concrete inspection chamber.
The concrete inspection chamber is neither technically nor economically advantageous and it can be considered a mere expense.